首页 / 行业
博世德累斯顿晶圆厂投资超10亿欧元
2022-06-01 14:48:00
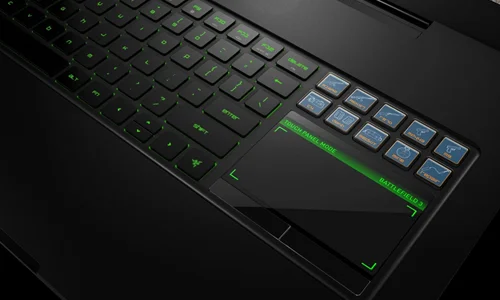
上期,我们走进了博世半导体生产基地——德累斯顿晶圆厂,一同见证博世半导体产品诞生的全过程。
本期,我们将揭晓德累斯顿晶圆厂高效生产的秘诀,解码全球最前沿的生产技术!
全自动生产的秘诀 —— 智能物联网
德累斯顿晶圆厂之所以能实现高效的自动化生产,离不开两种前沿技术的相互作用——人工智能(AI)和物联网(IoT),两者结合就形成了智能物联网(AIoT)。德累斯顿晶圆厂是博世集团首个智能物联网工厂,在工厂中,晶圆被智能物联网引导着,在一百多台机器上有序历经数百个处理步骤。
得益于物联网技术的应用,所有系统、传感器和产品产生的数据都被集成在中央存储库中。人工智能算法则可以通过与数据库的比对,检测到产品中出现的微小异常。异常出现后,专家团队就能立即对原因进行分析并及时纠正,从而保证产品的稳定性和可靠性。这是进一步改善制造工艺和半导体质量的关键,也使得半导体产品可以在更短的时间内进入量产阶段。此外,人工智能算法还可以自我学习,并根据数据进行预测,从而精确预测产线设备进行维护和调整的时间,大大节省时间和成本。依托于智能物联网,博世以数据驱动持续改进,为生产奠定了良好的根基,并成为了工业4.0的全新标准。
复制一个线上工厂 —— 数字孪生
在德累斯顿晶圆厂施工的过程中,工厂的所有部分以及与工厂相关的全部施工数据都以数字化形式被记录下来。建筑物、基础设施、供应及处置系统、电缆管道、通风系统、生产设备以及整个工厂的所有其他部件都以3D(三维)模型的方式进行可视化处理,使整个建筑及所有流程都被精确地映射到一个三维模型中。这个虚拟的数字世界,就是“数字孪生”。德累斯顿晶圆厂的数字孪生工厂囊括了约50万个3D对象,这使得所有升级改造工作都能够在线上进行流程的模拟及优化,无需干预现实世界中正在进行的操作。
从其它地方看到德累斯顿——智能AR眼镜
为了更好地对“数字孪生”工厂及生产流程和数据进行可视化管理,博世在德累斯顿工厂应用了AR(增强现实)技术。透过智能AR眼镜,专家们能够清晰地看到叠加在现实环境之上的数字化内容。博世开发的AR应用程序将晶圆厂的能源数据显示在“数字孪生”中,从而通过可视化追踪和分析来优化制造机械的碳足迹。智能AR眼镜还可以帮助推动施工计划和进行机器和系统的远程维护,安装在数据眼镜上的摄像头甚至可以将视频图像同步传输到世界其它地方,使来自世界各地的设备制造专家可以实时指导德累斯顿的技术员,无需亲临现场就能进行技术维护。
如今,全球新下线的每辆汽车中平均搭载了约20颗博世的芯片,包括动力控制系统、安全气囊、制动系统、停车辅助系统等等。随着自动驾驶系统和电动汽车的飞速发展,汽车行业将需要更多、更强大的芯片。博世投资超10亿欧元建设的德累斯顿晶圆厂正是博世对半导体应用领域需求激增的回应。结合多种前沿生产技术,完全数字化和高度自动化的德累斯顿晶圆厂将持续深耕汽车芯片制造,为计划、生产和交付提供更加高效的解决方案。
审核编辑:彭静最新内容
手机 |
相关内容
智能传感器助力打造数字经济数字世
智能传感器助力打造数字经济数字世界,数字,经济,传感器,助力,智能,及时发现,PCM1801U智能传感器是一种能够感知环境并将感知结果转不只是芯片 看看传感器技术我们离
不只是芯片 看看传感器技术我们离世界顶级有多远,传感器,芯片,位置,测量,交通,用于,传感器技术是现代科技中至关重要的一部分,它们被工业物联网数据采集:从Modbus到MQTT
工业物联网数据采集:从Modbus到MQTT,数据采集,物联网,模式,网关,协议,数据,工业物联网(Industrial Internet of Things,IIoT)的核心任务消除“间隙”:力敏传感器如何推动新
消除“间隙”:力敏传感器如何推动新颖的HMI设计,传感器,智能手机,交互,交互方式,操作,用户,随着科技的不断发展,人机交互界面(HMI)的设射频前端芯片GC1103在智能家居无线
射频前端芯片GC1103在智能家居无线通信IoT模块中应用,模块,芯片,无线通信,智能家居,支持,数据交换,射频前端芯片GC1103是一种低功耗所有遥不可及,终因AI触手可及
所有遥不可及,终因AI触手可及,出行,平台,无人驾驶汽车,导致,人工智能,学习,人类历史上,有许多事物曾被认为是遥不可及的,然而随着科技面向6G+AI,鹏城云脑的演进
面向6G+AI,鹏城云脑的演进,鹏城,人工智能,数据存储,脑可,智能终端,智能,随着科技的不断进步,人们的生活方式也在不断改变。6G+AI(人工阿里平头哥发布首颗SSD主控芯片:镇
阿里平头哥发布首颗SSD主控芯片:镇岳510,平头,芯片,物联网,性能,阿里巴巴,支持,阿里平头哥是指阿里巴巴集团的CTO张建锋,他在宣布了阿