首页 / 行业
数字化工厂实践的经验分享
2019-06-29 11:31:00
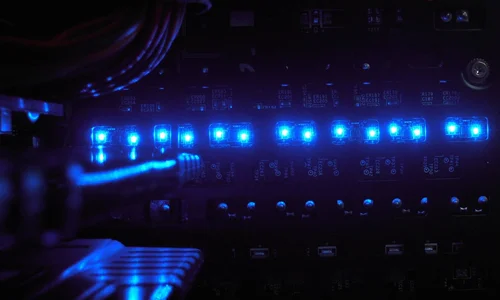
“企业智能化要经历计算机化、连接、可视、透明、预测和自适应六个发展阶段,然而,目前面临着五大问题和挑战:一、自动化设备覆盖率低;二、装配环节基本靠手工;三、质检过程缺乏先进手段;四、信息化建设存在断层,车间管理成为“黑匣子”;五、供应链各相关环节信息“孤岛”。”在2019年6月13日-6月14日由勃肯特冠名的“2019(第二届)高工机器人集成商大会暨十佳集成商颁奖典礼”上,广东利元亨智能装备股份有限公司研究院院长杜义贤就数字化工厂实践作了主题发言。
杜义贤表示,数字化工厂是由数字化模型、方法和工具构成的综合网络,通过连续的没有中断的数据管理集成一起,最终要实现的是所有生产过程可视化、数字化呈现。他特别强调,数字工厂并不等于无人工厂。
数字化工厂是一个复杂的系统,又没有统一明确标准的定义,需要结合行业、企业自身进行定制实施;而综合性工作开展面临着风险和较大投入,如何构建一个符合企业自身的数字化工厂,是否可以提前虚拟体验?在数字化的落地实践中,利元亨有哪些先进的技术和经验分享?
数字化是智能工厂的基础
“数字化是智能化的基础。”杜义贤说。
在杜义贤看来,真正的智能是从预测开始,下一步会产生什么问题,数据背后会产生什么问题,真正做到智能化的要求是一个系统可以自动应对发生的问题。然而,目前大部分的企业在智能化的布局中都还处于计算机化的阶段,数据还在收集的过程中,并未涉及到分析数据产生的原因和这些数据可以给我们带来什么。
在数字化工厂的推进过程中,基础条件是精益生产成熟度、流程成熟度、管理运营及IT水准,战略以及顶层规划设计。从自动化产线到自动化车间再到智能工厂,经历精益化、自动化、数字化、智能化层层推进,从而实现全面高端制造。
数字化落地实践
杜义贤首先介绍了利元亨在数字化工厂方面的实践之一,即2D工程仿真运作,采用2D工厂布局,导入仿真计算软件,并设定运作数据和物流,进行工厂布局验算推算人员安排、物流流畅性、设备使用率、AGV需求量等工厂运作数据。
在2D工厂仿真运作中,关键技术点包括:1、多系统联合调度:集成AGV/WMS/WCS/产线系统等,如何模拟集成这些生产系统,并快速运作推算生产数据;2、人员与设备运作推算:工厂的运作由多个工站组成,如何处理各工站的故障率、生产节拍需要使用大数据推算,而不是简单的串联或并联计算可以得到符合实际;3、综合性IE规划:仿真人员需要具备生产管理、场地规划、各系统应用等技术才可以较为真实录入所需参数,使得仿真结果更加逼近真实运作;
杜义贤认为,整个系统要调动起来,包括AGV、WMS系统和WCS系统,需要工厂级的信息和调动能力,需要有大量的工业实际基础和信息库的支持以及IE的思考。
基于2D工厂仿真运作,利元亨还建立了3D工厂的仿真运作,从更细节的方式提供工厂的设计,在这个平台上,能够呈现出关于未来数字工厂的模型,包括自动组装的区域、检测区域的布置,来料的过程和人工的安排,都是一目了然。
3D工厂仿真最重要关键技术有三点:1.快速建模:单机3D模型少则100多个零部件,多则上千个零部件,整个工厂建模工作量巨大,如何快速建模成为是否可以体现工厂模型的关键技术之一;2.模型简化:单机3D模型存储容量小则500M,大则超过1G,整个工厂模型如生搬硬套的对接搭建,将会导致整个模式存储容量巨大,对于软件和硬件要求极高;3.快速定义:整个工厂的涉及成百上千的信号驱动,如何让工厂按照预定的生产规则仿真运行起来。
利元亨拥有企业云—设计库,产品涉及多个领域,有丰富机构案例库,快速构建前期方案模型,提高建模速度;并且还有专职模拟快速处理软件开发团队20人,将100G模型压缩至1G,压缩100倍,标准队伍28人,开发多个快速模型定义软件。
“我们企业设计库叫利元亨云,搭建三维模型库非常快,跟搭积木一样,另外我们有专业的技术团队,有压缩的模拟仿真软件。”杜义贤如是说。
在3D工厂仿真的基础上,利元亨进一步进行产线布局。在整个产线中,物流和工位节拍是最为重要部分,也是利元亨一直关注的部分。据悉,利元亨收集一千多万条生产数据,建立了参数计算平台,节拍计算准确度精度可达95%,并自动生产节拍表。
杜义贤指出,产线仿真运作关键技术点:1.物料流程仿真:模拟整个物料流转过程,实现生产过程实时分析;2.工位节拍精度:多个运动部件关联,验证产线生产节拍是否符合要求;3.多设备衔接验证:产线设备多物流衔接,合理分配各机台的产能节拍、故障率等分析。这其中还涉及到设备元器件多样化、控制方式多样化、多系统交互。
在车间漫游模式下,通过人机交互的方式点击虚拟设备按钮,可以进入自动化设备数字同步阶段。
在数字化同步上,利元亨数字孪生技术真正做到了虚实同步、数据同步和模拟换型:将3D模型与真实设备连接,实现3D模型跟随真实模式运动,解决环境限制问题,提高设备运作过程可视化;设备运作过程产生的数据在3D模型上直观的展示出来,以便于维护人员快速定位和判定设备问题,如设备报警;将新产品的换型参数导入3D模型,模型根据换型参数离线模拟设备动作过程,降低新产品换型错误导致损坏产品、设备碰撞等异常的发生。
现场,利元亨还展示了其数字孪生技术演示平台,该平台集成了云技术、移动app应用、边缘计算、机器视觉识别等关键技术,实现了让客户可以使用移动设备远程下达需求订单,设备可以根据订单进行个性化产品生产,同时在移动端实施展示设备实际运行情况,让客户可以远程查看定制产品整个实际生产过程,了解产品生产情况和进度。
在设备同步之后,利元亨建立了园区的数字化服务,实现了数字化车间的同步,园区发生的事情可通过3D模型进行展示。
在底层,利元亨做了一个数字化采集系统,该系统有几个特色:1、数据追溯可靠:提供壳诉回溯追踪,原料、工序、设备、设计等可能不良原因的追溯查询;2、生产调度:集成RGV的生产调度功能;3、功能丰富:包含实时监控、生产数据分析、报警统计分析等十余项功能;4、数据传输采集高效:兼容主流PLC通讯接口,稳定高效率采集数据;5、安全可靠:通过指纹(人脸)识别操作人员的权限,并记录其操作设备内容;6、系统兼容性高:集成对接MES/制程排产/远程运维等生产管理系统接口。
依托于掌握了集成智能方案所涉及的多个领域通用平台技术,如工业机器人的多种应用、视觉应用、智能控制、信息系统、光学检测、激光焊接等技术优势,利元亨专门为新能源、汽车部件、精密电子、轨道交通、安防行业提供数字化、自动化、智能化整体工厂解决方案。
最新内容
手机 |
相关内容
智能传感器助力打造数字经济数字世
智能传感器助力打造数字经济数字世界,数字,经济,传感器,助力,智能,及时发现,PCM1801U智能传感器是一种能够感知环境并将感知结果转FPGA学习笔记:逻辑单元的基本结构
FPGA学习笔记:逻辑单元的基本结构,结构,单元,逻辑运算,数字,信号,结构单元,FPGA(Field-Programmable Gate Array)是一种可编程逻辑器件Efuse是什么?聊聊芯片级的eFuse
Efuse是什么?聊聊芯片级的eFuse,状态,编码器,故障,加密,芯片,配置信息,Efuse是一种可编程的电子熔断器,用于在芯片级别实现非易失性存应用在智能空调中的数字温度传感芯
应用在智能空调中的数字温度传感芯片,数字,芯片,温度,智能,数据,实时,数字温度传感芯片是一种用于测量环境温度的MAX3243CAI集成电浅析可配置混合信号芯片
浅析可配置混合信号芯片,芯片,信号,混合,配置,灵活性,性能,MC33072DR2G可配置混合信号芯片是一种集成电路(IC),它包含了数字和模拟电路浅析CD4094BE芯片在电路中的应用及
浅析CD4094BE芯片在电路中的应用及特点,芯片,键盘,数字,引脚,移位寄存器,控制,CD4094BE是一种串/并转换器和8位移位寄存器芯片,主要数智城市共建下,数字基础设施将无处
数智城市共建下,数字基础设施将无处不在,数字,经济发展,智能,平台,能源,数字化,随着科技的进步和数字化的浪潮,数智城市的建设已经成什么是时间数字转换器,时间数字转换
什么是时间数字转换器,时间数字转换器的组成、特点、原理、分类、常见故障及预防措施,数字,分类,输入,信号,时钟,故障,OPT3001DNPR时